Product Loss Case Study Summary
Continuous online BOD monitoring improves product loss control and treatment plant efficiency D LeBlanc
Abstract:
American Milk Producers Inc. (AMPI) in Dawson MN wanted a reliable way to identify increases in their organic loading to optimize their treatment plant operation while reducing down-drain losses due to spills or leaks the process. The use of an on-line BOD monitor is described and results of reducing product loss within the factory.
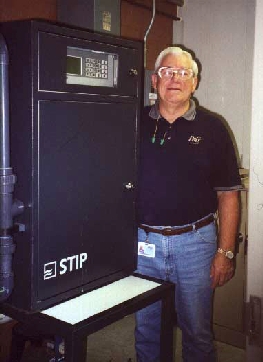
Loss Prevention and Waste Management from Processing Plants A new look at an old problem Author: Rob Dexter, Director, DCM
Abstract:
The real cost of product losses to drain on most production facilities is often greatly underestimated by management. As a result, expenditure of time and money to implement an effective loss prevention and management system is correspondingly inadequate. This paper will look at:
- The actual cost of losses from several Dairy and Food manufacturers and the methodology and cost required to implement an effective loss prevention strategy.
- Data representing losse, using various on-line sensing systems, specifically parameters such as Biological Oxygen Demand (BOD) and Chemical Oxygen Demand (COD) used in combination with flow, Suspended Solids (SS) or Turbidity (Turb) and pH.
- Actual gains achieved through the availability of this data to appropriate plant personnel and the cost/benefit ratio of each system with respect to the products present in the drains.
- Downstream management options such as diversion control and feed forward management of induced air flotation (IAF) and dissolved air flotation (DAF) systems.
Click to request a copy of full article
Beverage Industry uses Isco/Stip Phoenix Thermcat TOC analyzer to monitor effluent discharge for COD, D LeBlanc
Summary:
The Isco/Stip Phoenix - Thermcat provides reliable, continuous monitoring of effluent discharge for COD at a beverage factory. It eliminated the delays receiving laboratory results while correlating extremely well with Procter & Gambles in house laboratory results. Proctor & Gamble have purchased the analyzer and are in the process of interfacing it with their in-house SCADA system to provide automated discharge control.
Click to request a copy of full article
Effluent Control at a Fruit Juice Manufacturing Plant in Germany, S Patsch
Abstract:
Waldnieler Fruchsaft GmbH was able, due to the high automation of the plant, to ensure that the discharge values always meet the given official standards. Due to the application of the Isoc-Stip COD analyzers the analyzing time and with it the batch time of a cleaning cycle were reduced significantly. This has created additional capacity. In the past a sampler of the cleaned waste water had to be extracted and checked manually in the laboratory after each cleaning cycle. Now this test is completely automated. Also, storage of the data and initiation of further steps is an automated process. The plant operates largely independently from the operating personnel. Only the "Spill Tank" has to be filled manually which is done by switching the pump. And this only has to be done during operational tests.
Continuous Short-time BOD measurement - minimization of product losses and waste water loads in Dairy production, P Kalte (Gross-Umstdat) ; J Wimmer (Wasserburg)
Summary:
Whiler product losses in food processing can never be eliminate, Meggle MulchIndustrie, a dairy plant in Wasserburg, Germany, has found a novel way to reduce product losses and hence reduce BOD loading and energy costs at its WWTP. Assessment was made of whether to use pH, Turbidity, Conductivity, Density, COD or BOD as the monitored parameter to aid loss reduction. It was decided to install a rapid BOD monitor integrated with pH and conductivity sensors to locate the origin of the spills. The BOD monitor detects the spills within minutes and triggers an alarm. The plant supervisor determines the reason and origin of the spill which can then be stopped immediately. This system has resulted in a significant reduction of product losses and has drastically reduced BOD loads and electricity costs for the WWTP.
Proven experience with on-line COD measurement within the chemical industry; Dr C Genner
Summary:
The use of holding tanks to prevent COD discharges outside of consent levels at a chemical factory is described. On-line COD measurement with a measurement result in minutes is used to optimize the use of the divert tank and ensures a more consistent organic load to the lo-cat receiving municipal treatment plant. At another chemical manufacturing site on-line COD measurement has been used to relate peaks to events occurring within the factory. In addition the COD data has negated the need for tankering off site material since discharge to sewer is possible without exceeding the discharge license. Major revenue savings have resulted, around £16,000 per year, whilst also providing greater confidence that limits imposed are not exceeded.
On-line COD Measurement at Lactose NZ ; M McGuire-Barnes
Summary:
On-line COD monitoring at Lactose New Zealand (NZ) is an integral part of the LNZ loss monitoring system. Loss calculations are based on COD values and then multiplied by the flow rate to give the lactose loss rate. The previous system based on the use of the automatic samplers proved labor intensive and unreliable. Loss monitoring has provided the following:
- Financial data on losses
- Aid in prevention of losses
- Data for process improvement projects
- Validation of process parameters such as drain times, flush times etc.
- Identify problems and assist to reduce them
- Support control and improvement of environmental issues
- Aid in environmental impact reduction